Presenting the First Indigenous Indian Seismic Instrumentation System
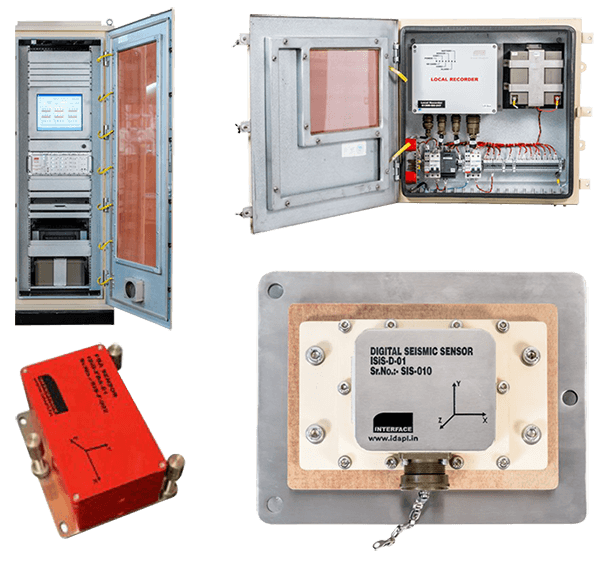

IdeaSIS is a indigenous technology developed by BARC and transferred to our company. The system is designed to continuously monitor the seismic activity and based on the same, alert the control room to take necessary action. IDAPL is executing the first system in the field, which will be implemented at RAPP 7&8 site of NPCIL.
To mitigate the seismic hazard, a Nuclear Power Plant (NPP) is designed to withstand the effects of vibratory ground motion arising from strong earthquakes. The design basis ground motion (DBGM) for this purpose is evaluated for each site. The DBGM is characterized by Peak Ground Acceleration (PGA), response spectral shape and a time history compatible with response spectrum. PGA and response spectrum are derived based on site specific studies. The DBGM parameters are evaluated for two levels of severity, S1 level earthquake or OBE and S2 level earthquake or SSE. The structures, systems and components (SSC) of the nuclear reactors are designed for either SSE (Safe Shut down Earthquake) Level or OBE (Operation Basis Earthquake) level earth quake.
After Fukushima incident it has become a regulatory requirement to have Automatic Seismic Trip System (ASTS) in nuclear reactors on detection of earthquake. This is designed to scram the reactor upon the occurrence of a seismic event, before turbine trip or other conditions resulting from the seismic disturbance could cause a scram. The earlier scram could give a lead time between 5 to 20 seconds. This lead time could provide resulting benefits such as reduced loads during the seismic event and, therefore, fewer burdens on the plant systems. It may also reduce the likelihood of a Loss of Coolant Accident (LOCA) or severe transient after a seismic event.
The main purpose of Seismic Instrumentation for Nuclear reactors is to generate automatic trip whenever an earthquake occurs beyond the design basis. Also it is required to record the acceleration history in order to do the post evaluation so that regulatory authority can take suitable decision regarding the restart of the reactor after Seismic Trip.
Strong motion seismic instrumentation at the Nuclear Power Point (NPP) consists of Seismic Switches and Seismic recorders. Seismic Switches are used for generating automatic trip signal to the Nuclear reactor and the data from the Seismic recorder is used for post earthquake analysis. In this analysis, the data from the Seismic recorder is compared with the design model to see the validity of the analysis as well as to check the exceedence of the design basis earthquake. Based on this analysis the decision is taken on restarting of the reactor.
The Seismic switch triggers on detecting the acceleration greater than the preset PGA level and generates auto trip signal for safe shut down of NPP. The PGA level setting is normally kept as the PGA of the OBE level response spectrum of the respective NPP sites. In a reactor building each floor is provided with a local seismic recorder (LSR) (sensor and recording unit). LSR’s can record data from 3-axis MEMS acceleration sensor mounted inside when the Seismic Switches are triggered. Local
Seismic recorders are also configured for level triggering. This means an LSR is continuously monitoring its 3-axis acceleration data and records if any axis acceleration crosses a preset acceleration level. for example 10mg .
A Central Seismic Recorder (CSR) is connected to all LSR’s through a communication link. Graphical User Interface (GUI) software in the CSR can configure each LSR during installation. The recorded data from the LSR are also transferred to CSR periodically. CSR is having a large storage capacity (1 TB or more) in its external hard disc. These data are time tagged in real time with the help of a stable local clock always accurately synchronized to Universal Time Reference by latching on to an improvised GPS (Global Positioning System) receiver.
The system has been qualified to meet the stringent NPCIL standards as per PC-E-403 specifications. The following qualification tests have been performed and the system has cleared it successfully:
ENVIRONMENTAL TESTS
1. Dry heat test : IS-9000, Part-III ,1977
2. Damp heat test : IS-9000 Part-V Section 2 – 1981
EMI/EMC TESTS
1. Conducted Emission Test: IEC-61000-6-4
2. Radiated Emission Test : IEC-61000-6-4
3. Voltage dips, Short Interruptions and Voltage Variations Test: IEC-61000-4-11
4. Test for Immunity to Conducted Common Mode Disturbance: IEC-61000-4-16
5. Immunity test for Harmonics & inter-harmonics: IEC 61000-4-13
6. Electric fast transients: IEC-61000-4-4
7. Conducted Disturbance induced by RF fields: IEC-61000-4-6
8. Power frequency Magnetic Field Test: IEC-61000-4-8:
9. Radiated Electromagnetic Field: IEC-61000-4-3
10. Electrostatic Discharge: IEC-61000-4-2
11. Combinational Wave or High Energy Surge Immunity: IEC-61000-4-5
SEISMIC QUALIFICATION TEST
1. Seismic test of the system on the shake table
2. 5 times OBE and 1 time SSE test
ISiS-D-01 Seismic Sensor


- Ruggedized Field Mounted unit
- IP65 enclosure ( IP68 optional )
- MIL grade connector
- Sensor type : MEMS technology
- Measuring Range : ± 2g, + 4g, + 8g
- Dynamic Range : 120 dB ( 144 dB optional )
- Frequency response : 1 KHz
- Orientation : Tri-Axial , Horizontal Floor Mounting
- Self test Option: Available
- Non-linearity : ≤ 0.3% F.S.
- Operating Temperature : -5°C To 85°C
- Humidity : 100% RH
- Output : Digital Signals for X, Y & Z ( Analog optional )
Analog output option also available with + 10 V - Optional:
- In-built battery ( for 7 day backup )
- In-built memory for 7 day backup ( system can work off-line also )
- GSM based communication
- GPS based timing
- Mounting Accessories
- Calibration software for laptop based tuning
ISiS-FBA-01 Force Balance Accelerometer

- Number of axes: 3 axis
- Orientation: Horizontal or vertical (wall mount)
- Levelling: Manual, with adjusting knobs
- Casing: Solid machined Al enclosure powder coated
- Dimensions: 140x155x85mm
- Weight: 3 kgs
- Protection grade: IP68
- Tolerated humidity: 0-100%
- Temp. operative range: -20 to +70°C
- Bandwidth: standard DC-100Hz;
- Damping: 0.7
- Inertial mass weight: 15 g
- Standard sensitivity: 5 V/g (2g at full scale)
- Output impedance: 100 ohm
- Full scale: +2 g (standard, +1 g or +4 g optional )
- Output: +/-10V fully differential (50 ohm)
- Dynamic range: > 165dB (From 0.1Hz to 20Hz with 1g full scale version)
- Noise floor: < 80 ng √Hz
- Power supply: 10-15Vdc (80mA for a triaxial unit in standby)
- Connector: Mil grade connector
- Optional:
- In-built battery ( for 7 day backup )
- In-built memory for 7 day backup ( system can work off-line also )
- GSM based communication
- GPS based timing
- Mounting Accessories
- Calibration software for laptop based tuning
Seismograph / Local Recorder


- Resolution : 20-24 bits
- Operating temperature range : -5 °C to +85°C
- Works with 3 channels: X,Y & Z data channels
- Sampling rate : 4k samples per second
- Timing : Internal high precision RTC
- GNSS/GPS optional
- Event Triggers offered: PGA or CAV on any of X,Y or Z axes or combination
- Recording :
- Pre-event Recording – 1 to 15 steps in steps of 1 second (User settable)
- Post-event recording – 1 to 15 steps in steps of 1 second (User settable)
- External trigger also available
- Recording capacity : 32GB maximum
- Relay outputs: 4 nos.
- Communication : Dual isolated RS485 ports for redundant connectivity
- Data format : ASCII, MINISEED formats
- Battery back up: 72 hour battery backup
- Self Test facility : Available
- Rugged enclosure : EMI/EMC, IP65 and Seismic resistant enclosure EMI/EMC proof polycarbonate viewing window
- Power supply to sensors : 12-30 Volts as per sensor requirement
- Input power : AC/DC options 72 hour battery backup
- Software : User friendly setup and diagnostic software
Central Recording Server System


- Industrial PC based system
- Ruggedized 19” rack panel EMI/EMC and seismic qualified
- Connectivity : Max 9 seismographs
- Fault tolerant Redundant architecture for communication channels
- User Friendly modular software supporting ASCII, MINISEED
- Software computations :
- Peak acceleration
- Response spectrum
- Time history
- Cumulative absolute velocity (CAV).
- User Friendly Routines for parameter settings, calibration & testing of sensors and
- seismographs
- Provides event triggers in the range
- Axes used : X,Y or Z of any LR or logical combination of 3 channels
- Data storage in standard formats
- 72 hour battery backup